Automatic Milking: How Effective Is It?
They have been the topic of discussion for some time now, but as they become increasingly popular, Charlotte Johnston, TheCattleSite junior editor, looks at just how effective automatic milking machines are and evaluates their benefits.A common myth regarding automatic milking machines is that they disengage the herdsman from the animals, and so neglect herd health.
If this were true, the new Lely Astronaut A3 Next would not have won the 2009 Royal Association of British Dairy Farmers' Livestock and Machinery Award at this year's Dairy Event. The award was presented on the grounds of economics, the welfare and close management of milking animals, the reduction of drudgery for family and employed staff, flexibility since it applies to family run and larger units, and the longer-term needs of the dairy industry.
TheCattleSite spoke to four dairy farmers around the world to find out how automatic milking equipment changed their lives. Click on Tim Gibson, Doug Heintz, John Wolf and Max Warren to read about their experiences.
How Does it Work?
Very simply, a laser control will identify the location of the teats and a robust robot arm will attach cups individually to each teat from underneath the cow. Swift teat cup attachment is guaranteed even when milking cows with teats missing. Should a cup be kicked off, it is reconnected quickly.
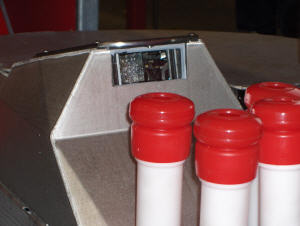
Each cow has an electronic tag, which is read when she enters the machine. This allows the computer system to identify each cow. Management through the computer tells the stockman specific data for each individual cow.
The MQC sensor system checks the milk colour, conductivity and flow to ensure maximum control of milk quality. Comparing individual cow data to the average allows problems to be identified.
Milk identified with blood is separated and either discarded or diverted into another holding place.
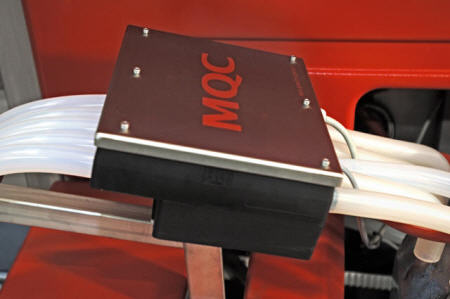
Furthermore, if a cow is being treated with medicine, it is possible for her to remain in the milking herd. This does require strict attention to detail - as accurate information must be input into the computer system as to what the cow has been treated with, how long the withdrawal period is etc. When the cow comes in to be milked next, her milk will be automatically diverted into a separate holding area or disposed of. The same can be done for colostrum, for example, when a cow has recently calved as it may be beneficial to retain the colostrum for a couple of days. Entering all information on the system will allow this milk to be stored separately and after two days, her milk will return to the bulk tank.
By checking the computer twice a day, the stockman can identify cows that are overdue milking or can treat illnesses identified immediately and the accessibility to such detailed data can allow accurate management decisions to be made.
Dynamic feeding looks at an individual cow's feed requirements in relation to her yield. The programme takes into account milk yield, the cost of feed and the milk price received to work out the most economical feed rate for each individual cow. For Max Warren in Australia, this is particularly useful in a drought situation, where extra feed may have to be bought, but when milk prices are particularly low.
On average in the UK, for every litre of milk produced per cow, 0.3kg of dry matter is consumed, says Tim Gibson. This is standard regardless of whether they are high yielders. He believes he has saved one kilo of dry matter per cow per day, which with 140 cows equates to more than 51 tonnes of dry matter a year – in other words, a lot of money!
John Wolf and Doug Heintz from the US say that they now have the ability to feed a higher concentrate diet to higher yielding cows and they believe they have reduced feed costs.
The dynamic feeding programme allows optimum energy conversion efficiency. This unique and efficient system would not be possible without automatic milking machines.
All four farmers have cut back labour units. In Australia, Mr Warren believes he would require double the number of staff to milk 300 cows on a rotary system. Mr Wolf is saving 200 hours of labour a week, whilst Mr Gibson and Mr Heintz have cut back by almost one labour unit each. Adding up the cost of current labour, it is not hard to see how much money can be saved.
Lely estimate that for every one machine milking 70 cows, half a labour unit is saved. Two robots would milk 140 cows and save three-quarters of a labour unit, whilst three machines would milk 200 plus cows and save one full labour unit.
"The biggest advantage by far is the labour saving. The flexibility has changed my life allowing me to spend more time with my family," says Mr Heintz.
Mr Gibson recommends that an area of approximately 15ft by 12ft is needed. The machines, however, are only 15ft by 6ft; the extra space takes into account a clean area behind the machine. With so little space required per machine, customers have the opportunity to increase indoor housing.
Controlled grazing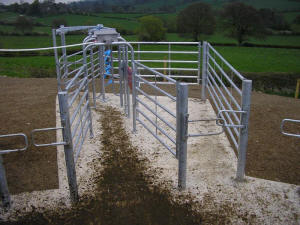
Both Mr Wolf and Mr Heintz keep cows housed all year round; only dry cows and heifers may be put to grass. Mr Gibson allows his cows to graze outside during the summer with controlled grazing. Unlike the other farmers, Mr Warren's cows are grazed outdoors all year around on a three-way grazing system.
Previously, Mr Warren operated a two-way grazing system, where cows moved paddocks every 12 hours. He found with this system that cows were hanging around the parlour and so he changed the process to a three-way grazing system. Now, cows move fields every eight hours, each time passing through the parlour. Cows are fed a wagon mix in the shed and fed concentrates when milked. All pasture is irrigated.
Training herd to use machine
Mr Wolf said that it takes about three to four days to train heifers to use the machines. However, when the machines were introduced, it took about three weeks before things were running smoothly. He believes that there will be about 0.5 per cent of each herd that does not adapt. Mr Heintz says that he spent three weeks pushing cows up to the machines, but it probably took about three months until the machines were working at full efficiency.
Over in Australia, Mr Warren says that it took two to three weeks to train the herd to walk into the robots but he felt it was probably twelve months until he was fully trained to use the system, the technology including computers was completely new to him!
Herd Benefits

The Lely Astronaut has a refined udder preparation procedure. Teats are cleaned individually and sprayed. The machine also automatically washes three times a day as well as washing in between each cow.
At the Robotic Dairy in Australia, cows are lasting six lactations. Further improvements in herd health can be seen by Mr Gibson reporting an increase in lifetime lactations per cow. Mr Wolf and Mr Warren reported improvements in foot health and reproductive performance.
Mr Heintz, who believes he had high standards of animal health prior to the installation of the machines, has reported no significant improvements in herd health but said that previous levels had been easily maintained. He has also only been using the machines for just under a year.
Walking around Mr Gibson's yard, it was apparent that the cows seemed dramatically calmer and at ease than in an conventional dairy unit. In fact, all farmers mentioned that cows were a lot less stressed, which in turn they believed led to better health and increased yields.
Increased yields seemed apparent across the board but the improvement varied between farms. In the UK, Mr Gibson reported an increase of 1,000 litres per cow over the last eight years, whereas Mr Heintz reported an increase of 10 to 15 pounds per day over the last ten months, which equates to 4562.5 pounds of milk per year or about an extra 2,000 litres per year.
Service and Installation
The same system operates in the US and the UK with Lely providing onsite support for the first 2-3 days of training cows. During the first two to three weeks, representatives will call in three or four times a week to help with the start-up. Chad Huyser, Director of Sales and Operations for Lely US, says that farm management support staff will visit a couple of times during the first few months to do a thorough review of the farm management process, which includes making slight adjustments to feed rations and robot performance settings. Mr Gibson, who completed farm management training in Holland with Lely, says that he goes onto clients' farms to help customers adapt to the new style of management and prevent problems.
Lely also offer web training events with the farm management support staff, providing information to farmers on how to use the T4C, which is the onboard management software on the robots. Mr Huyser says that one of the areas that Lely focuses on globally is providing on-going support to all their installations.
* "Automatic milking is not just another way to milk cows, it is another way to manage the farm." |
Tim Gibson, Hunters Hill Farm
|
The new Lely Astronaut A3 robotic milking system requires servicing three times a year. Mr Gibson says the older models require servicing every eight weeks. He says that information from each service is sent back to a database at the headquarters, which allows engineers to access a vast amount of data to refer to in the case of a fault.
Due to the relative newness of the machines, there is no guarantee how long they will last. Mr Gibson believes that the oldest one in place is approximately 17 years old and still going strong. There have been no reports of machines wearing out to date. Lely estimates that products with the correct service and care will last at least 30 years. Machines can be constantly updated with new software, which comes at no extra cost to the customer.
Some people may be under the impression that robotic milking systems require someone to be on call 24/7 in case of a breakdown. This is not technically true. If there is an error in the system, an alarm system rings a telephone to tell whoever is on duty. During the day, this is not a problem but during the night, it could be more than a nuisance.
Not one of the farmers complained about this. During the evenings, Mr Gibson and Mr Warren said their machines may go off once a week. With seven machines, Mr Wolf is called three or four times a week. Mr Wolf stressed that the system can be manipulated and managed to reduce these calls through only five minutes of maintenance per robot per day.
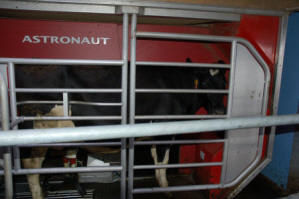
How Much Does it Cost?
The latest model, Lely Astronaut A3 Next, is around £110,000 for one robot. Opportunities for second-hand robots exist: all robots are refurbished at the Lely factory and come with a one-year warranty. Mr Gibson says that they often become available due to clients upgrading or retiring and cost approximately 75 per cent of the new price.
Farm Benefits
Mr Wolf explained that the introduction of robotic milking machines has allowed greater flexibility across the farm - particularly with regard to time schedules. "Having the robots in place means that I can now finish what I was doing in the field without rushing back to the parlour to milk the cows," he said. Mr Wolf also stressed that the working environment has significantly improved with cleaner areas for both cows and employees. But by far the biggest benefit for him was the decreased costs of production.
When asked about the biggest benefit of installing a robotic milking system, Mr Warren said the fact he was still farming. "Without robots, I would have stopped milking years ago. I really enjoy working with automatic milking machines and Lely. I love the technology that is always improving. It makes my work so much more enjoyable and interesting."
* "Justification for how well the machines are working - seven months later we bought two more!" |
John Wolf, Maple Lawn Farm
|
Who Supplies Automatic Milking Machines?
If you are interested in robotic milking systems, Lely, BouMatic, Fulwood, DeLaval and GM Liberty are some of the suppliers.Management Tips
And finally, some tips from Mr Gibson, Mr Wolf, Mr Heintz and Mr Warren:
- Run your cows numbers and cash flow and make sure that the operation and introduction of robots into your herd would be viable
- Design the layout of the facility to how you want to manage it
- When designing the layout, consider if you may want to expand the enterprise and make sure this is possible
- Be prepared for a change in management
- Make sure you are prepared to get involved with the robots, checking data and ensuring careful attention to detail
- Be sure that whoever is supplying the machines will provide long-term full technical support, and
- See as many farms as possible and speak to as many people as possible before making any rash decisions!
Despite the success in Australia, to date there are still only six units operating automatic milking systems, which Mr Warren finds unbelievable. Despite the excellent support from Lely, Mr Warren is disappointed in the lack of support from the local dairy industry in Australia.
Robots have started to take off in America and Canada, as well as across Europe. In the UK, Lely is running 250 robots on over 100 units. Worldwide there are 9,000 Lely robots. So if you fancy reducing the drudgery of milking or simply improving herd management, whilst increasing milk yields and herd health, perhaps it is time for you to open your mind to automatic milking systems?