Attributes of sterilizing-grade air and gas cartridge filters
The key attributes to consider when selecting sterilizing-grade air and gas filtersOverview
Sterilizing-grade air and gas cartridge filters are used in critical applications in the food and beverage industry, to remove microorganisms from air or other gases such as nitrogen or carbon dioxide. Microbial contamination would otherwise negatively impact product quality causing problems such as sensory or nutrient quality degradation, reduced shelf life, spoilage or even hazards to human health. In some applications, unwanted microbial and bacteriophage contamination can impact process yield.
While much focus is placed on microbial retention, there are several other attributes of sterilizing-grade air and gas filters which are of high importance because they are an indispensable contributor to the success of the filtration. Filter manufacturers do extensive validation work to test and document all aspects of expected filter performance.
Sterilizing-grade filters must feature:
- Microbial Retention
- Hydrophobicity
- Low Resistance to Airflow
- Robustness
- Suitable Geometry
- Integrity Testability
- Application Compatibility
- Absence of Toxic Substances
- Documented Validation, Quality and Traceability
This article describes the key attributes to consider when selecting sterilizing-grade air and gas filters. Figure 1 illustrates a typical sterilizing-grade air filter cartridge.
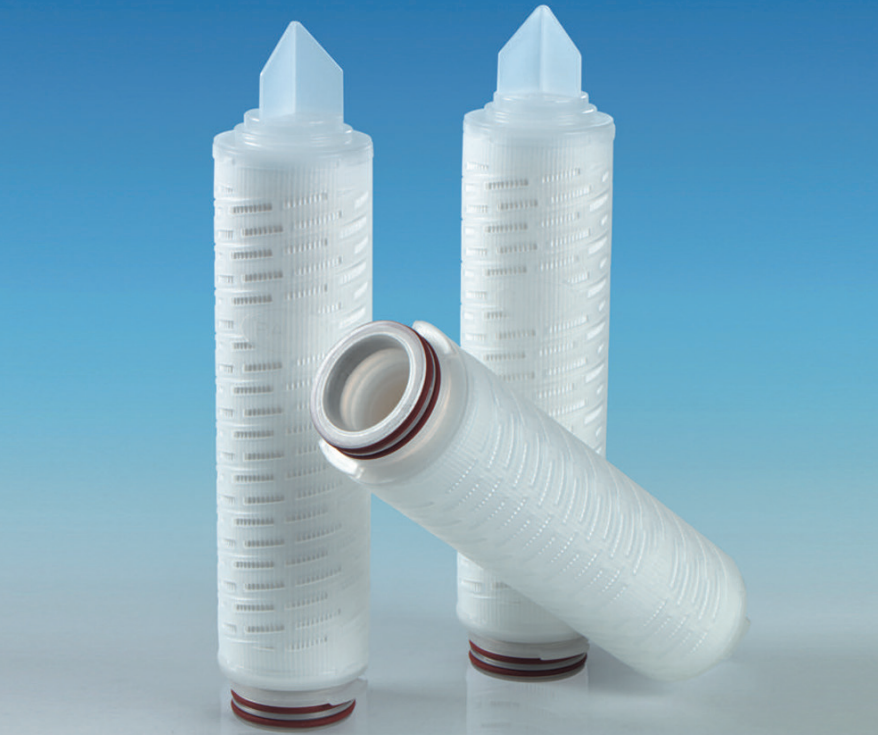
Microbial Retention
Microbial retention is the single most important performance attribute of sterilizing-grade air filters. If the required sterility in a critical application cannot be achieved, the primary goal of the filtration fails. The FDA’s Guidance for Industry (1) specifies, that a sterilizing-grade air filter is one which has been validated by the filter manufacturer to show the reproducible retention of the model microorganism Brevundimonas diminuta (ATCC 19146), when the filter is challenged at an area challenge concentration of 107 colony-forming units (cfu)/cm2 of effective filtration area, yielding sterile effluent, or zero viable microorganisms found in the filtrate. This model microorganism was chosen due to its small size of approximately 0.3 micron (µm) mean diameter. This definition points to the need for microbial validation testing, rigorously applied to test filters in development, production-scale sample filters, and to deal with material or production changes that could impact filter performance. “Evaluating Microbial Retention Performance in Sterile Air and Gas Filters for the Food and Beverage Industry (2)” provides a further detailed discussion about microbial validation.
Figure 2 shows a scanning electron micrograph of a 0.2 µm membrane filter surface with B. diminuta rod-shaped bacteria (3). Note that the diameters of the pores are not all equal to 0.2 µm: Many pores are larger than 0.2 µm while others are smaller than 0.2 µm; they are distributed around a mean. Bacteria cells penetrate some distance into the membrane depth, throughout which they are captured, due to the mechanisms of air filtration (4).
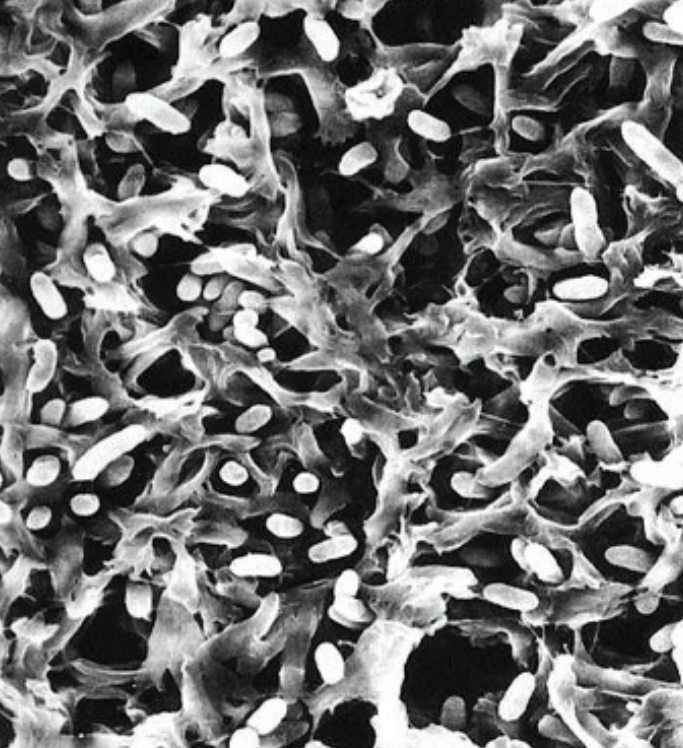
An additional important consideration is the type of validation carried out, i.e., whether filter microbial retention performance is based on liquid challenge or aerosol challenge testing, as the outcome of filtration is greatly influenced by whether a liquid or a dry gas is being filtered. “Liquid and Aerosol Bacterial Challenge in Sterile Air Filter Validation (5)” describes filtration performance under these conditions and the methods used to validate this performance.
Aside of the basic bacterial challenge test which establishes the capability of filters to sterilize air, filter manufacturers may include validation work to further illustrate the filters’ fit for purpose, such as demonstrating filter retention of bacterial spores, long-term aerosol bacterial challenge, and aerosol bacteriophage removal.
Hydrophobicity
Hydrophobicity is a physical property that refers to the lack of affinity of a material for water. A hydrophobic material will reject repel, rather than absorb moisture. Material have different degrees of hydrophobicity, measured as dynes/cm to express critical surface tension values of different materials.
Materials selected for air filters should display a high degree of hydrophobicity, meaning they remain dry in the presence of moisture in the air. This is important because filters with low hydrophobicity will partially or fully wet out in the presence of steam condensate or moisture in the air, and thus hinder airflow. In a compressed air installation, a wetted filter can provide such a high barrier to airflow that it may collapse due to the resulting high differential pressure between upstream and downstream pressure. Another advantage of hydrophobicity in air filters is a quicker drying or “blow down” time after steam sterilization or integrity testing techniques utilizing a wetting agent.
Of the typical materials of construction used for filter media in sterilizing-grade air filters, PTFE exhibits the highest degree of long-term hydrophobicity. There are sterilizing-grade cartridge air filters that are constructed with PTFE media, while others are constructed of different materials that are impregnated with PTFE or alternative substances to render them hydrophobic. It is important to note that due to the rigorous steam sterilization cycling that these filters undergo, attention should be given to whether the filters maintain their hydrophobicity over the duration of their service life.
In compressed air applications, instances of partial wetting of hydrophobic filter pores can occur regardless, especially in cases of process upset. It is possible to have “hydrophilic spots” that can compromise the success of the filtration if the filters have only been validated on aerosol challenge claims (2,5).
Low Resistance to Airflow
Low resistance to airflow is a highly desirable attribute of sterilizing-grade air filters, as it translates to more compact installation sizing. Aside of the air resistance resulting from the filter cartridges themselves, especially in high airflow applications, the filter housing configuration (inlet/outlet connections, design) takes on an increasing importance in keeping airflow rates high and resulting pressure drops low. In general, achieving low pressure drop on compressed air applications saves on compressor energy.
Filter media allows airflow due to its porosity or void volume, i.e., the open area in a filter. The higher the porosity, the lower the airflow restriction. Higher filter area does not necessarily equate to higher airflow. Given a certain type of material and amount of filter area, porosity is influenced by the thickness of the filter media fibers or filaments: the thinner the fibers the greater the media porosity (Figure 3).
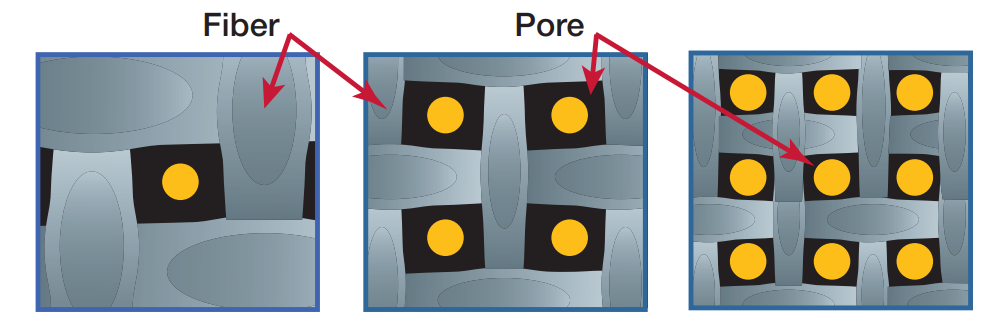
Fiber Pore
Pore sizes also influence airflow: the more open the pore sizes within the filter media, the greater the airflow. Greater airflows are commonly seen in depth filters as compared to membrane filters because of their larger and wider distribution of pore sizes.
Porosity is expressed as a ratio of airflow divided by clean pressure drop. It is important to note the different airflow characteristics based on the application supply pressure: the greater the air supply pressure, the greater the airflow at a given clean pressure drop (Figure 4).
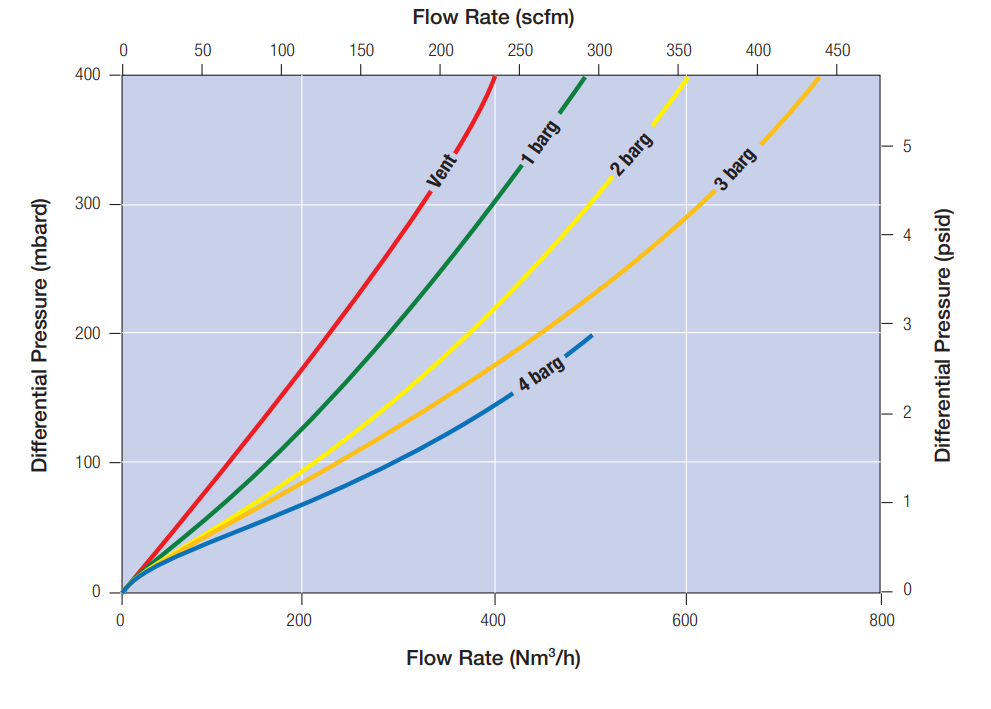
Robustness
Sterilizing-grade air filters are subjected to repeated in-situ steam sterilization heating and cooling cycles in operation, hence they must be extremely robust in their design. Filters are validated to withstand a certain number and length of steaming cycles in forward and reverse direction; these can be in the range of >100-200 cycles and 0.5-1 hour cycle lengths, without compromising their retention performance.
Steam sterilization is the greatest stressor to the filter, as the media softens at high temperatures. The change of temperature will also stress the cartridge due to the different rates of expansion and contraction between the different materials of construction.
Another stressor is high differential pressure across the filter: filters must be validated to demonstrate maximum forward and reverse differential pressure resistance during operation.
Users must not exceed filter manufacturer limits for proper steaming cycle frequency, length and temperature in forward or reverse direction, differential pressures, and operating temperatures.
The durability of a filter is influenced by its design and materials of construction of the filter media, support and drainage layers, hardware and sealing materials. Manufacturing methods used to join various components of the filter cartridge together, such as adaptors, end caps, cage, and core, as well as methods for sealing cartridge sections together also influence robustness.
Suitable Geometry
Sterilizing-grade air filters should be of single open-end design. An adaptor design with a twist-lock connection, double bayonet design, two O-rings, and an internal adaptor ring, as well as a cartridge locating fin is recommended. A tight seal of the filter adaptor to the housing prevents unfiltered air bypass during operation, and along with the locating fin affords good physical stability of the cartridge during steaming and normal forward or reverse operation. Threaded connections in the adaptor area are not recommended due to hygienic design concerns. Figure 5 illustrates the components of a typical sterilizing-grade air filter cartridge.
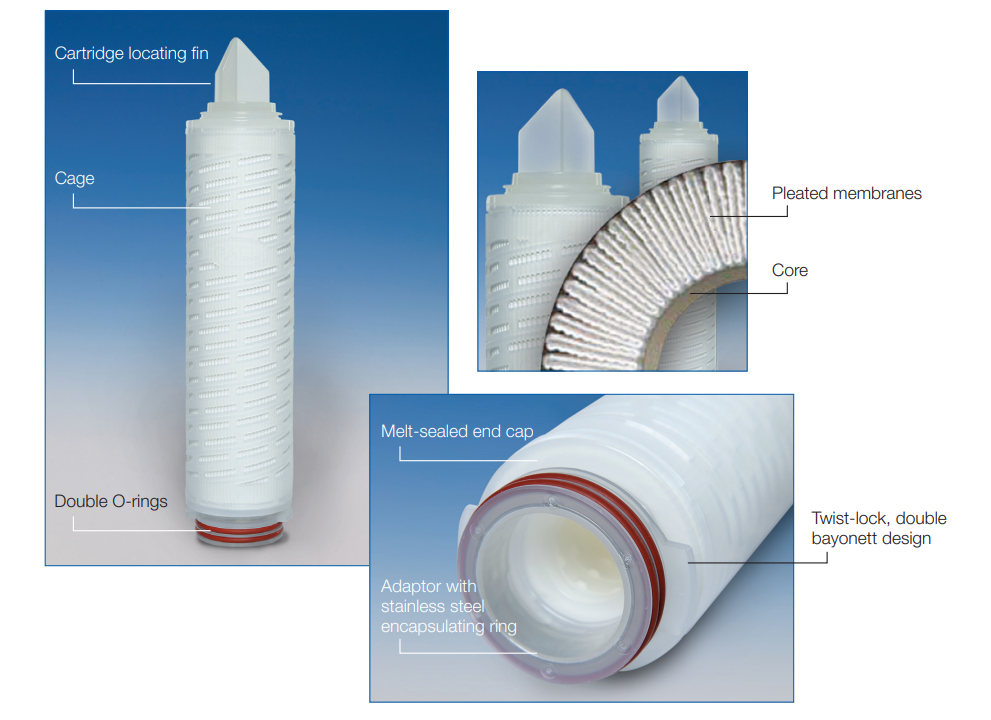
Integrity Testing
Microbial retention validation is a destructive test. A correlation to this test is necessary to enable verification of filter performance in operation. Such a non-destructive test, called an integrity test is a necessary tool for users of sterilizing-grade air filters. Manufacturers define an integrity test pass/fail value that correlates with the filter’s microbial removal efficiency; this correlation applies a suitable safety factor. An integrity test can detect even minute damage in the filtering medium, seal and hardware of the cartridge that is not visible to the human eye. Ideally, integrity testing should be used before and after production, to reduce the risk of batch failure.
Application Compatibility
During their service life, sterilizing-grade air filters are exposed to air for many months up to a year or longer. Their materials of construction must be validated to be oxidation-resistant at the expected time duration and temperature conditions of use. The materials must also be compatible with the expected type, temperature and concentrations of any other chemicals (e.g., hydrogen peroxide) which may be present.
Degradation due to incompatibility of filter materials with the application impacts the integrity of the filtration, initially evidenced by a failed integrity test. Extreme degradation of the filter media, support and drainage layers into a white powder may become physically apparent.
Absence of Toxic Substances
Filter materials of construction should not release any toxic substances into the product or onto productcontacting equipment surfaces. Filter materials should satisfy national and international regulations for direct or indirect food contact use.
Documented Validation, Quality and Traceability
The validation work done by a filter manufacturer to substantiate filter performance claims is described in detail in a document called a ‘Validation Guide’ or ‘Technical Performance Document’ or similar. The specific validation testing includes information about the tested attribute, the numbers and configurations of filter samples tested from different lots of normal production batches, detailed test methodology, and results of these tests and concluded filter performance claims. This work forms the basis for the performance data given on product data sheets.
Manufacturing release criteria should include a successful integrity test for each filter prior to shipment, and full traceability to production records and vendor materials by serial numbering of filter modules. A robust quality assurance program must be implemented to provide reproducibly high-quality products to fully satisfy customer needs and expectations.
Summary
Sterilizing-grade air and gas filters are used in critical filtration applications so they must satisfy stringent performance and quality expectations. By reviewing the necessary attributes of sterilizing-grade filters, users are better positioned to make the right selections for their applications.
References | ||||
---|---|---|---|---|
1 Food and Drug Administration. Guidance for Industry – Sterile Drug Products Produced by Aseptic Processing – Current Good Manufacturing Practice; CDER, CBER, ORA: Rockville, MD, September 2004. Accessed at https://www.fda.gov/downloads/Drugs/Guidances/ucm070342.pdf. | ||||
2 Pall Corporation. Evaluating Microbial Retention Performance in Sterile Air and Gas Filters for the Food and Beverage Industry. 2020. | ||||
3. Osumi et al., PDA J. Pharma. Sci. & Technol., v. 50: pp. 30-34, 1996. | ||||
4. Pall Corporation. Mechanisms of Air Filtration. 2020. | ||||
5 Pall Corporation. Liquid and Aerosol Bacterial Challenge in Sterile Air Filter Validation. 2020. | ||||